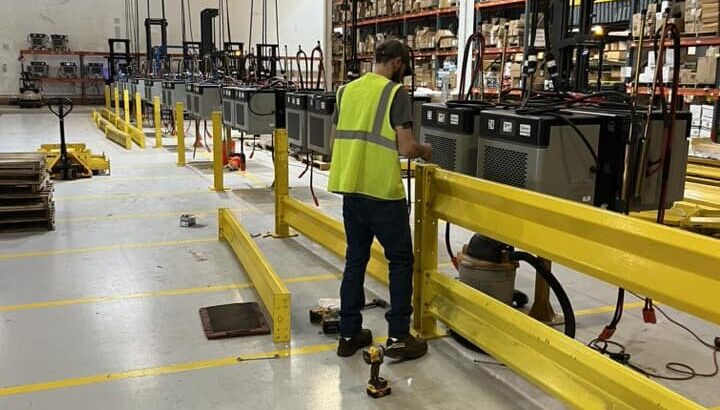
Table of Contents
ToggleAs you explore ways to enhance efficiency in your industrial projects, mobile welding is a pivotal solution, blending on-site convenience with robust capability. Its ability to reduce downtime and adapt swiftly to project demands offers a significant edge. Yet, it’s not without its hurdles; prioritizing safety and managing the complexities of mobile operations are challenges you’ll need to navigate. As we unpack these layers, consider how integrating mobile welding could shift your project dynamics, especially when tackling the balance between immediate benefits and the foresight required for seamless execution.
Benefits of Mobile Welding
Why consider mobile welding for your industrial projects? This method offers unparalleled flexibility by enabling on-site fabrication and repairs, significantly reducing downtime. You’ll find that the on-site convenience of mobile welding enhances time efficiency and streamlines the completion of your urgent or scheduled repairs. You’re no longer at the mercy of transporting heavy or large components back and forth; everything is handled right where you need it.
Moreover, the flexibility provided by mobile welding allows for immediate adaptations during the project. Industrial projects can shift rapidly, with unexpected needs arising. Mobile welding applies to these changes swiftly, ensuring that your project timelines are met without compromising the integrity or quality of the work.
The quality assurance aspect can’t be overstated. Mobile welding units are equipped with skilled technicians who bring the workshop to you. These professionals are well-trained in the latest welding techniques and safety standards, ensuring each weld is executed to the highest quality. Their expertise becomes an integral part of your team, fitting seamlessly into your project’s ecosystem, and fostering a sense of belonging and unity among all project stakeholders.
Operational Challenges
Navigating the operational challenges of mobile welding requires a deep understanding of both logistical complexities and technical constraints. Prioritize safety procedures to protect your team from potential hazards inherent in mobile environments. Regular equipment maintenance is crucial; it ensures your welding machines and tools function optimally, preventing downtime and ensuring high-quality output.
Skill training can’t be overlooked. You’re a welder and an adept problem solver, capable of adapting your expertise to varied and unpredictable conditions. This adaptability is key as you face diverse materials and structures, often under time-sensitive circumstances.
Project coordination is another significant hurdle. Have a robust strategy to manage the logistics of moving equipment and personnel efficiently. On-site logistics, from ensuring the availability of power sources to the strategic placement of welding units, require meticulous planning and foresight.
In your role, you’ll find that every site has unique challenges, from restricted spaces to environmental conditions that impact welding processes. Your ability to anticipate these issues and plan accordingly enhances efficiency and strengthens your sense of belonging within the team, as everyone relies on your expertise to navigate these complexities successfully.
Cost Analysis
Assessing the costs of mobile welding projects involves a detailed analysis of direct and indirect expenses. You’ll need to dive into specific cost comparison metrics highlighting the efficiency advantages of mobile versus traditional in-shop welding setups.
Direct costs primarily include labor and materials. However, the efficiency of mobile welding can significantly reduce labor hours with on-site work, thereby enhancing your savings potential.
When considering indirect costs, think about the transportation of materials and equipment. Here, mobile welding brings substantial savings as you cut down the frequent back-and-forth between shop and site, which eats up time and fuel. These efficiency advantages often tilt the budget considerations in favor of mobile welding.
Moreover, let’s talk about the broader financial impact. Mobile welding drastically reduces downtime, as repairs and fabrications occur right where the infrastructure is situated. This reduction in downtime not only accelerates project timelines but also minimizes revenue loss, contributing positively to the overall financial health of your project.
Case Studies
Let’s examine specific case studies that demonstrate the effectiveness and cost-efficiency of mobile welding in various industrial scenarios. By taking a closer look, you’ll see how these instances not only highlight the adaptability of mobile welding but also underscore the tangible benefits it delivers.
- Bridge Construction in Rural Areas: Mobile welding teams expedited the assembly of bridge sections, ensuring project success despite the remote location. On-site solutions proved critical in avoiding delays typically caused by transporting prefabricated structures.
- Oil Pipeline Repairs: Mobile welders were promptly deployed when leaks were detected in a critical oil pipeline. Their on-site presence and skill flexibility allowed immediate and effective repairs, enhancing efficiency improvements and ensuring minimal downtime.
- Automotive Manufacturing Retrofit: Mobile welders efficiently integrated new robotic systems into existing production lines. This case showed how on-the-spot welding could adapt to complex, changing requirements while maintaining high standards of client satisfaction.
- Shipyard Maintenance: During peak periods, additional mobile welding units were brought in to handle the increased workload, demonstrating significant adaptability and contributing to overall project efficiency and success.
- High-rise Building Construction: Mobile welding facilitated the quick setup and modification of steel frames, crucial for meeting tight project deadlines and achieving high levels of client satisfaction through skill flexibility and effective on-site problem-solving.
These cases are clear testaments to the strategic advantages of incorporating mobile welding solutions into diverse industrial projects.
Future Outlook
As industries continue to evolve, the demand for mobile welding is expected to grow, driven by its proven flexibility and efficiency in diverse settings. You’ll find that technology advancements are pivotal in shaping the future landscape of mobile welding.
Innovations such as automated welding robots and enhanced power sources are set to increase productivity, allowing you to tackle more complex projects with greater accuracy and less downtime.
Moreover, as market demand escalates, there’s a crucial need for specialized workforce training. You’re part of a community that values upskilling and staying ahead means embracing continuous learning that adeptly handles newer technologies and materials. This ensures that your skills remain indispensable in an increasingly competitive field.
Sustainability practices are also becoming central to mobile welding operations. You’ll be expected to adopt eco-friendly techniques that minimize environmental impact, aligning with global shifts towards greener industrial processes.
Complementing this, stringent safety regulations are being introduced to ensure that as you adapt to new methods, your workplace remains safe. You need to understand and implement these regulations to protect yourself and your colleagues from potential hazards inherent in welding tasks.
This holistic approach enhances efficiency and fortifies the community’s commitment to quality and safety.
Frequently Asked Questions
What Safety Certifications Are Required for Mobile Welders?
You’ll need certifications addressing welding processes, safety gear, training requirements, inspection standards, and legal compliance to ensure you’re fully prepared and protected. These validate your expertise and adherence to safety protocols.
How Does Weather Impact Mobile Welding Operations?
Weather conditions greatly affect mobile welding operations, influencing productivity, equipment maintenance, and safety precautions. Adapting welding techniques to counteract adverse weather ensures continuity and safety in your community of welders.
What Is the Average Setup Time for Mobile Welding Equipment?
How quickly can you start welding on-site? Typically, setting up mobile welding equipment takes 30-60 minutes, depending on setup efficiency, equipment maintenance, safety protocols, and project scheduling for on-site repairs.
Are There Specific Insurance Policies for Mobile Welding Businesses?
You’ll find specific insurance policies for mobile welding businesses, including liability coverage, workers’ compensation, property insurance, commercial auto, and equipment protection, ensuring all aspects of your operations are comprehensively safeguarded.
Can Mobile Welding Be Used for Underwater Projects?
Yes, you can dive into underwater welding, but it requires specialized equipment, extensive training, and an awareness of environmental considerations. The project’s limitations hinge on these factors, ensuring you’re well-prepared for the challenges.
Conclusion
As you navigate the intricate landscape of mobile welding, it’s a high-stakes chess game where strategic moves in safety, equipment management, and logistical planning determine success.
Embracing these challenges can transform potential setbacks into powerful advantages, trimming costs and enhancing operational efficiency.
By staying ahead with innovative strategies and thorough analysis, you’ll ensure that your industrial projects are successful and future-proof in the ever-evolving field of mobile welding.